Functionalizing Agents
Functionalizing agents are additives that improve the properties of the polymer or confer characteristics that the original polymer does not possess. Adding functionalizing agents extends the range of applications for which polymers can be used, and enables the range of applications of individual polymers to be widened. The types and characteristics of typical functionalizing agents are described below.
Plasticizers
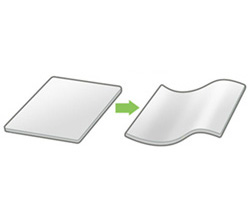
Plasticizers bridge the gap between polymer molecules and weaken their intermolecular forces, giving greater freedom of movement to each molecular chain. This lowers the glass transition point of the polymer and imparts it flexibility. In particular, the flexibility of polyvinyl chlorides can be readily controlled by varying the amount of plasticizer added, and PVC can therefore be adapted to a large number of applications. Since plasticizers are blended into the polymer in large amounts, their compatibility with the polymer must be good. In addition, plasticizers need to have a number of advantageous properties, such as low volatility, strong heat resistance, and good weatherability. Therefore, various plasticizers that possess these properties have been developed
Epoxidized Vegetable Oils: Epoxidized Soybean Oil (ESBO) and Epoxidized Linseed Oil (ELSO)
These oils also function as stabilizers and are therefore used as both plasticizers and stabilizers.
Phthalates: Dioctyl Phthalate (DOP) and Dibutyl Phthalate (DBP)
As the most versatile plasticizers, these are blended into many flexible polyvinyl chlorides.
Polymeric Plasticizers: Polymeric Dibasic Acids (Adipic Acid, Sebacic Acid, Phthalic Acid, etc.) and Glycols (1,2-Propanediol, Butanediol, etc.)
These have good retention, low volatility, non-migration properties, and excellent heat resistance, but are inferior to DOP in compatibility and cold resistance.
Nucleating Agents and Clarifying Agents
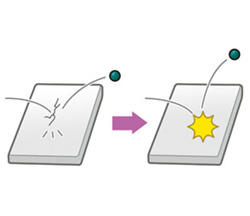
Adding a nucleating or clarifying agent to crystalline polypropylene polymer enables its crystals to take on a fine structure during molding. The addition of these agents therefore significantly improves mechanical properties such as flexural modulus and heat distortion temperature, and also increases transparency. It also improves the crystallization temperature, which leads to a shorter molding cycle, thereby contributing to improvement in production efficiency and cost reduction. These advantages make nucleating and clarifying agents multifunctional additives which function effectively in various fields.
Metal Carboxylates: Aluminum Para-Tert-Butyl Benzoate and Na Benzoate
These nucleating agents have been used for a relatively long time. They are effective for improving physical properties and crystallization temperature, but not for improving transparency.
Sorbitols: Dibenzylidene Sorbitol and Di-Alkyl-Benzylidene Sorbitol
Although their improving effects on physical properties are small, these function effectively as clarifying agents. Due to their poor thermal stability, they may decompose during molding, generating the odor of benzaldehydes, the raw material from which they are formed.
Phosphate Metal Salts: Phosphate Sodium Salts
These salts are most effective for improving physical properties and processability, and are also effective as clarifying agents. They have good resistance to heat and hydrolysis. Types with improved dispersibility have also been developed for applications requiring enhanced transparency.
Flame Retardants
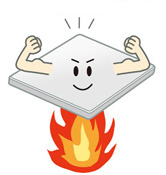
Flame retardants are used in applications in which there is a possibility of the polymer combusting as a result of exposure to high temperatures during use, such as the plastics used in electrical cables, electrical devices, and office automation equipment. The flame retardants developed to date can be classified according to their mechanism of action into: those that decompose and generate water and evaporative latent heat, thereby lowering the temperature of the polymer; those that prevent progress of the combustion reaction through chemical means; and those that form a foamed layer which acts as a barrier against heat and oxygen.
Antistatic Agents
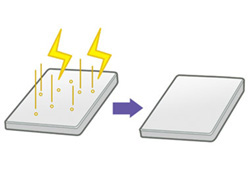
Since most plastics are insulators, they do not readily discharge the static electricity produced by various types of friction and are prone to static buildup. This makes plastics susceptible to adhesion of dust and dirt, resulting in serious problems such as noise generation in office automation equipment. To solve such problems, a large number of antistatic agents have been developed for use as coating or kneading-type agents in plastics. Most antistatic agents are based on surfactants that combine within their molecules a hydrophilic group for emission of electric charge with a hydrophobic group for improved affinity with the plastic.
Anionic Surfactants: Alkyl Sulfonates, Alkyl Benzene Sulfonates, etc.
Antistatic capabilities of these surfactants are inferior to the other types of surfactants.
Cationic Surfactants: Quaternary Ammonium Salts, Quaternary Ammonium Polymers, Alkylamine Sulfates, etc.
These surfactants have strong antistatic capabilities, and are used by kneading them into the plastic, or in the finishing process of synthetic fabrics. Quaternary ammonium salts exhibit superior antistatic performance, but suffer from the disadvantage of discoloration.
Nonionic Surfactants: Glycerin Mono-Fatty Acid Esters, Fatty Acid Diethanolamides, etc.
Because of their excellent heat resistance and good compatibility with polymer, these are used by kneading them into the plastic.
Amphoteric Surfactants: Alkyl Betaines and Alkyl Imidazolium Betaines
These can be used in either alkaline or acidic conditions. They have relatively good antistatic capabilities, but may cause discoloration problems when exposed to heat.
Lubricants
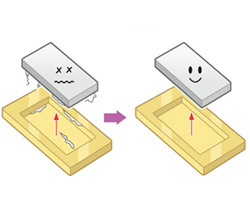
In the plastic molding process, lubricants reduce the friction between the plastic and processing machine, and between the plastic particles, and they are therefore effective for improving the fluidity and mold-release properties of the plastic, and for enhancing the processing efficiency and appearance of the resulting molded article. Some act as external lubricants, and some are effective for improving internal lubricity; typically, both types are used in combination.
Hydrocarbon Lubricants: Paraffin Wax, Synthetic Polyethylene, and Liquid Paraffin
These are typical external lubricants and are chemically stable.
Fatty Acids and Higher Alcohols: Stearic Acid, Behenic Acid, 12-Hydroxystearic Acid, and Stearyl Alcohol
Fatty acids act as external lubricants, while alcohols act as internal lubricants.
Fatty Acid Amides: Stearic Acid Amide, Oleic Acid Amide, Erucic Acid Amide, Methylenebis (Stearic Acid Amide) and Ethylenebis (Stearic Acid Amide)
The acid amides are used for polypropylene (PP) and polyethylene (PE), while the alkyleneamides are used for polyvinyl chloride (PVC), polystyrene (PS), and acrylonitrile butadiene styrene (ABS).
Metallic Soaps: Ca, Zn, Mg, and Pb salts of Stearic Acid
These are used not only as lubricants but also as stabilizers for PVC. In polyvinyl chlorides, the Zn and Pb salts are used as external lubricants, and the Ca and Mg salts are used as internal lubricants.
Esters: Glycerin Monostearate, Glycerin Monooleate, Butylstearate, etc.
These possess both internal and external lubricity.