The Safety Quartet
The Safety Quartet is a concept developed and proclaimed uniquely by the ADEKA Group to guide the safe operation of its business activities. It consists of four types of safety: occupational safety, environmental safety, quality safety and equipment safety. The ADEKA Group adheres strictly to the Safety Quartet, sharing information on it globally, to execute duties efficiently Group-wide. In fiscal 2020 the Group is pursuing activities related to four targets corresponding to the Safety Quartet: simultaneous achievement of zero labor accidents, zero environmental accidents, zero quality complaints and zero major equipment failures. The Group advances the Basic Principles of the Safety Quartet described below by continuously improving through the PDCA cycle (Plan, Do, Check, Act), attaining ever-higher levels to achieve one’s goal. In particular at Safety Quartet Review Meetings conducted at the end of each fiscal year, each department and section will be evaluated as to whether it has implemented its plans based on division policy and specific measures, after which divisional policy and specific measures for the next fiscal year will be decided.

1. | Leadership |
2. | Compliance with laws, regulations and rules |
3. | Advancement of 5S |
4. | Communication |
5. | Life-cycle evaluation and analysis |
6. | Overview of the supply chain |
7. | Contribution to a sustainable social structure |
8. | Pursuit of new technologies |
● | The ADEKA Group is promoting the Safety Quartet(labor, environment, quality, equipment) worldwide, with a zero target in each category. |
● | The ADEKA Group contributes to communities as a global enterprise committed to a sustainable society. |
As part of efforts to foster a culture of safety and strengthen the Group’s safety foundations, in fiscal 2019 the ADEKA Group unified its regulations on the Safety Quartet into a single set of rules, changing related criteria and standards into a single, unified regulatory system. In fiscal 2020 the Group is establishing the Global Regulations on the Safety Quartet and applying them to overseas Group companies.
Sharing the Safety Quartet Worldwide
ADEKA is advancing activities to raise awareness of the Safety Quartet in all Group companies. From December 3 to 5, 2019, the Group hosted the first Safety Quartet Global Meeting. In this meeting, the safety managers of 14 overseas production companies met at Kashima Plant and Head Office to share information on on-site safety measures and approaches to safety.
In addition, the design and languages used in the Safety Quartet symbol were updated for worldwide applicability and the updated symbol was distributed as helmet stickers to all Group employees. A Safety Quartet poster was displayed and circulated by posting on the ADEKA in-house portal website.
Safety Quartet Promotional Framework
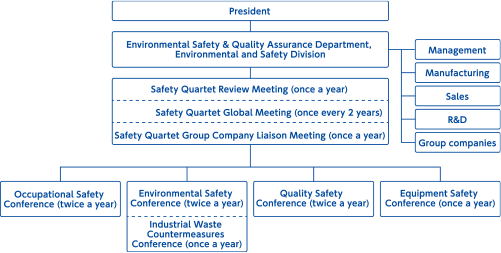
The Environmental and Safety Division conducts annual audits on all production and research facilities in Japan. In fiscal 2019 this practice was extended to four Group companies overseas. Through these audits, the ADEKA Group ascertains the status of safety management at each business location and cultivates a Group-wide culture of safety. In quality safety, the Group upgraded its product-liability audits, quantifying results using a unified checksheet for both chemical and food products. These audits were implemented at 29 departments and sections.
1.Occupational Safety
Security and Disaster Prevention
ADEKA Group production sites handle hazardous and toxic substances. Security and protection against disaster in the handling of these materials is a top Group priority. Determined to earn the trust of local communities, the ADEKA Group not only maintains strict compliance but also conducts rigorous safety management on its own initiative. Measures include thorough process management and equipment maintenance as well as regular, practical disaster-response training envisioning a wide range of disaster scenarios.
Occupational Health and Safety
The ADEKA Group recognizes safety as its most important issue. To improve employees’ safety awareness and create safe workplaces, the Group has switched over to the ISO 45000 occupational health and safety management system and is conducting activities via the Health and Safety Committees and the Zero Accidents Committees in each workplace. In efforts to prevent occupational accidents, the Group carried out safety experience training at Urawa R&D Laboratory (with 60 attendees in fiscal 2019) and established a Safety Experience Center in Fuji Plant (Shizuoka prefecture). The latter is slated to commence operation in fiscal 2021.
2.Environmental Safety
Initiatives on Global Warming Prevention
● Initiatives for Reducing CO₂ Emissions
ADEKA is committed to maintaining a stable supply of products while slashing CO₂ emissions and improving indices such as production efficiency. To confirm the progress of these efforts, the president conducts plant audits and the Environmental and Safety Division conducts audits of its own.
● Energy-Saving Activities
In fiscal 2019 ADEKA changed the lineup of goods it produces. As new equipment came into operation, our plants’ energy consumption increased. Thanks to energy-saving activities, however, we were able to reduce our energy consumption by 1,406 kl crude-oil equivalent.
Reduction of Environmental Impact
● Preventing Water Pollution
The protection of water resources and prevention of water pollution are indispensable to the formation of a recycling-based society. With this truth in mind, the ADEKA Group recaptures and recycles wastewater from its production processes. We also strive to reduce environmental impact from wastewater in accordance to laws and regulations.
● Preventing Air Pollution
The ADEKA Group implements various environmental-protection measures at its production and R&D divisions. In continuous measures to prevent air pollution, the Group makes committed efforts to restrain the release of sulfur oxides, nitrogen oxides and dust into the atmosphere.
● Properly Managing the Treatment of Industrial Waste
To ensure that the industry waste entrusted to them is treated appropriately, ADEKA and domestic ADEKA Group companies conduct regular inspections of industrial-waste treatment contractors. We also hold meetings on the status of waste management with each business location, including those of industrial-waste treatment contractors, to ensure that these operations are managed correctly.
● Promoting Biodiversity
Guided by the ADEKA Group Biodiversity Policy, the Group undertakes efforts to preserve biodiversity. The Group also participates in biodiversity initiatives as a member of the Japan Business Initiative for Biodiversity (JBIB) network member.
3.Quality Safety
● Reassessment of Quality Inspection Practices
From the 2017 to the 2019 fiscal year, the ADEKA Group has conducted a series of surveys on quality control. As a result, the Group confirmed that it had no cases of unqualified persons doing work that requires official qualifications, including inspection; and that there were no cases of intentional tampering of inspection and other data.
● Promoting Quality Improvement Efforts
To ensure that customers can use ADEKA Group products with confidence, the ADEKA Group has acquired certification under the ISO 9001 quality management system at 22 Group companies in Japan and overseas and is continuously maintaining and improving its quality assurance system. At its food production sites, the Group has acquired certification under FSSC 22000 (seven sites) and HACCP (three sites). The ADEKA Group is expending great efforts on food safety management and quality assurance.
4.Equipment Safety
In December 2018, ADEKA and domestic Group companies agreed on and began applying a definition for“ major equipment failure.”* Since then, these companies have continuously achieved a rate of zero major equipment failures.
* Definition of major equipment failure: Failure resulting in cessation of production for one week or more.